This article focuses on the technical characteristics of the application process of oxy-fuel combustion technology in the glass industry, summarizes the experience and conducts exploratory research on glass furnace construction, installation, heating-up, heat insulation and other technologies, and provides a forecast of the industry‘s future development in combination with cutting-edge technology.
1. Overview
1.1 Application and Development of Oxy-Fuel Combustion Technology in the Glass Industry
Glass products are an indispensable product in our daily life, and their industrialization and industrialization have a history of more than 100 years. Glass melting is actually a process of heating the pre-prepared raw materials to the corresponding temperature by burning fuel to generate heat. In traditional glass melting, oxygen in the air is used to assist combustion. As we all know, the composition of air is 20.9% oxygen, 78.1% nitrogen and 0.939% rare gas, 0.031% carbon dioxide, and 0.03% other gases and impurities. Therefore, when using air to assist combustion, only about 20.9% of the oxygen is effective. More than 78% of nitrogen and other components not only cannot generate heat, but will consume and take away a lot of heat during the combustion process.
Oxy-fuel combustion (also known as pure oxygen combustion) technology employs a combustion mode of fuel + oxygen, eliminating the energy waste and NOx pollution factors associated with nitrogen in air-assisted combustion. With advancements in oxygen production technology and reductions in electricity costs, pure oxygen combustion, composed of oxygen + fuel, has gradually replaced conventional air + fuel combustion methods. This is because oxy-fuel combustion offers unique advantages in environmental protection, energy efficiency, production output, product quality, reduced equipment investment, and savings in factory space.
As the benefits of oxy-fuel combustion technology in glass furnaces become increasingly evident, China has progressively expanded its research and application of this technology. Since 2001, with the commissioning of the first domestic CRT oxy-fuel furnace, forward-thinking enterprises and institutions have recognized the new direction of future combustion technology and have continued to increase their focus and investment.
In China, rapid economic growth has exacerbated energy and environmental challenges, making green economy, circular economy, and carbon neutrality trends in economic life. As early as the "12th Five-Year Plan for the Flat Glass Industry," the Ministry of Industry and Information Technology explicitly advocated for the widespread adoption of oxy-fuel combustion technology. The "National Development and Reform Commission Order No. 29 of 2019" further encouraged the promotion and use of energy-saving and environmentally friendly furnaces (including oxy-fuel combustion technology). Over the past 20 years, from 2001 to the present, oxy-fuel combustion technology has achieved rapid development in numerous high-temperature combustion fields. In the glass industry, it has been successfully applied in both daily-use glass and specialty glass sectors.
1.2 Common Glass Furnace Types in the Glass Industry and Their Characteristics
Glass furnaces are commonly categorized by type: all-electric glass furnaces, air-assisted combustion glass furnaces (regenerative, unit melters), oxy-fuel combustion glass furnaces, and hybrid heating glass furnaces.
Among these, all-electric glass furnaces heat glass through electrodes. All-electric glass furnaces are further divided into cold-top and hot-top technologies, with cold-top glass furnaces being more prevalent. Since most electric glass furnaces employ vertical melting technology, their melting tanks are typically deeper. This results in unique characteristics in glass furnace structure, refractory material selection, and steel structure design and installation.
As the most common traditional glass furnaces, regenerative furnaces have been widely adopted in China. Through generations of relentless effort, China has accumulated extensive experience in energy efficiency, longevity, and daily operation and maintenance of regenerative furnaces, with energy-saving technologies leading the world. Compared to other glass furnace types, the design, material selection, construction of regenerators, and matching of combustion systems are critical to their success.
Hybrid heating glass furnaces are typically used for harder-to-melt, higher-quality specialty glasses. These are also known as hot-top electric heating glass furnaces. They usually employ air-assisted or oxy-fuel combustion for heating the flame space, while electrodes heat the glass melt internally. Compared to All-electric glass furnaces, their mechanisms for melting, homogenization, and bubble removal differ fundamentally. Such glass furnaces require comprehensive consideration of flame space and electric heating structures, material selection, and heating system matching, presenting relatively higher technical challenges. Among these, technologies related to flame space and flues are largely consistent with oxy-fuel combustion glass furnaces.
1.3 Differences in Oxy-Fuel Glass Furnaces
First of all, the oxy-fuel glass furnace, compared to the traditional air-assisted combustion furnace, does not have a huge volume, the refractory material usage of the excessive regenerators. Instead, there is a much simpler flue structure.
Second, the crown treatment differs fundamentally. Traditional air-assisted combustion glass furnace crowns primarily use silica bricks, mostly laid in interlocking patterns, with brick thicknesses ranging from 300–500 mm and mortar joints of 1–2 mm. In contrast, oxy-fuel combustion glass furnace crowns predominantly use fused cast materials such as AZS, α-β, β, or ER1851, employing pre-assembled, single-ring non-interlocking, dry-laid designs without mortar joints.
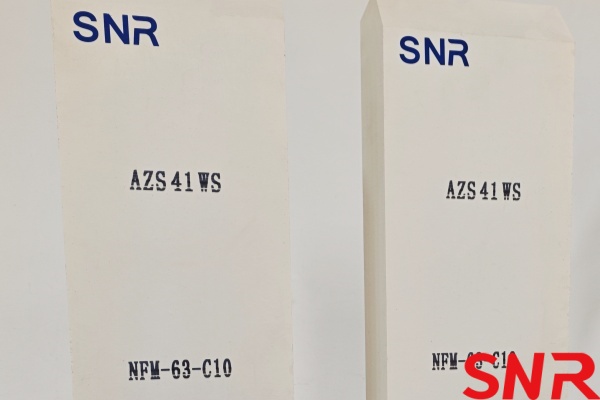
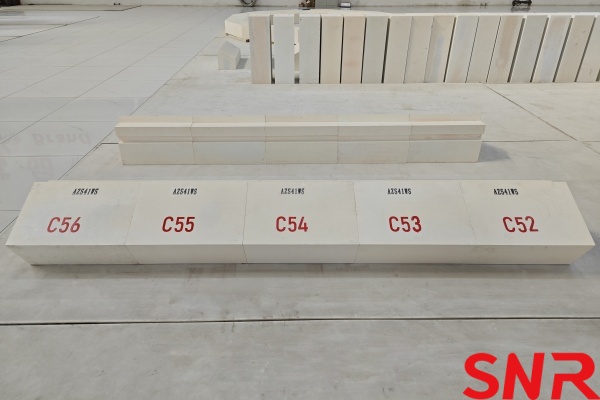
Since most daily-use glasses contain alkaline components, and the water vapor concentration in the exhaust gas of oxy-fuel furnaces is 7–8 times higher than that of air-assisted glass furnaces, the flame space and flue areas are highly susceptible to alkaline atmospheres and liquid alkali, which aggressively erode traditional acidic materials like silica bricks. Therefore, neutral or alkaline refractory materials such as fused cast AZS, α-β, β, ER1851, sintered AZS, zircon-mullite, corundum-mullite, or chrome-corundum are preferred for the flame space. The construction methods combine dry-laying and traditional bricklaying, posing new requirements for expansion design and construction precision.
2. Common Issues in Oxy-Fuel Combustion
As a relatively new technology, there are still few technical teams in China that fully master the design, refractory selection, pre-assembly, glass furnace construction, heating-up, charging, and heat insulation of oxy-fuel glass furnaces. Much of the knowledge is passed down orally, and domestic standards are still in the drafting stage.
Consequently, recent years have seen some accidents and detours in the development of oxy-fuel glass furnaces across the country.
The main issues observed in oxy-fuel glass furnaces include:
a. Glass quality failing to meet design requirements;
b. Energy consumption failing to achieve design targets;
c. Short furnace lifespan, failing to meet economic goals;
d. Environmental challenges, with some projects struggling to meet NOx emission standards;
e. Safety incidents, including explosions and backfire reaching valve groups;
f. Glass furnace safety issues:
- Crown collapse;
- Leakage at sidewalls, throat, or doghouse;
- Burn-through of breast walls;
- Bottom leakage.
This article focuses on glass furnace construction, so it elaborates only on the construction of key areas like the crown.
Compared to traditional air-assisted furnaces, oxy-fuel glass furnace crowns are dry-laid, mortar-free, and non-interlocking. Once problems arise, they are often fatal to the glass furnace.
In terms of ranking the safety of glass furnaces, the severity of problems that occurred ranked in order:
Crown collapse and bottom leakage are the most critical.
Leakage at sidewalls, throat, doghouse, working end, or distributor channels is next.
Burn-through of gable wall, breast walls, flues, or tuck stone.
Erosion or leakage in forehearths or feeders.
Bottom leakage, being irreversible, is equally critical in both oxy-fuel and traditional glass furnaces and will not be further discussed here.
For the crown, the dry-laid, mortar-free design makes any issue nearly irreparable (as evidenced by several domestic crown collapse cases). Thus, the crown is a focal point in oxy-fuel glass furnaces, requiring extra attention.
Below are some safety incidents from domestic oxy-fuel glass furnaces in recent years:
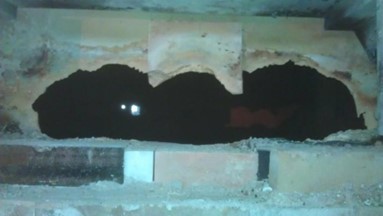
Case 1: Burn-through of a breast wall in a 2010 project.
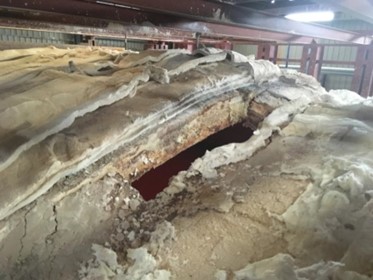
Case 2: Collapse of an oxy-fuel crown in 2018 (first of two collapses).
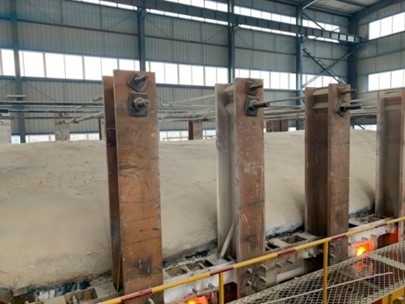
Case 3: Saddle-shaped deformation of an oxy-fuel crown in 2019.
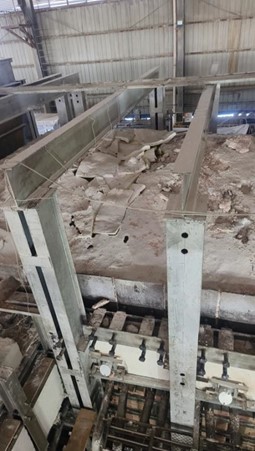
Case 4: Partial collapse of an oxy-fuel crown in 2023.
3. Construction of Oxy-Fuel Glass furnaces
3.1. Fabrication and Installation of Steel Structures
The steel structure of an oxy-fuel glass furnace primarily supports and secures refractory materials. Compared to traditional air-assisted glass furnaces, there is no fundamental difference. However, the crown skewback installation and adjustment require separate structures due to the single-ring crown design. Other aspects of glass furnace construction are technically similar.
Additionally, although fused cast materials have higher density, the crown design is thinner than silica bricks, so the overall weight of the crown in oxy-fuel glass furnaces is comparable to traditional glass furnaces. This also determines that the selection of materials for the columns and back seat beams do not need to be specially enlarged in design.
Since most oxy-fuel glass furnace breast walls and crowns are independent structures, tuck stone trays and lower support irons are not enlarged compared to traditional glass furnaces.
Issues like column deformation or jack screw bending due to steel structure miscalculations or adjustments during heating-up are similar to those in traditional glass furnaces.
3.2 Refractory block Construction
a) Crown Construction
As mentioned earlier, oxy-fuel glass furnace crowns primarily use fused cast materials and dry-laying, differing significantly from silica brick crowns.
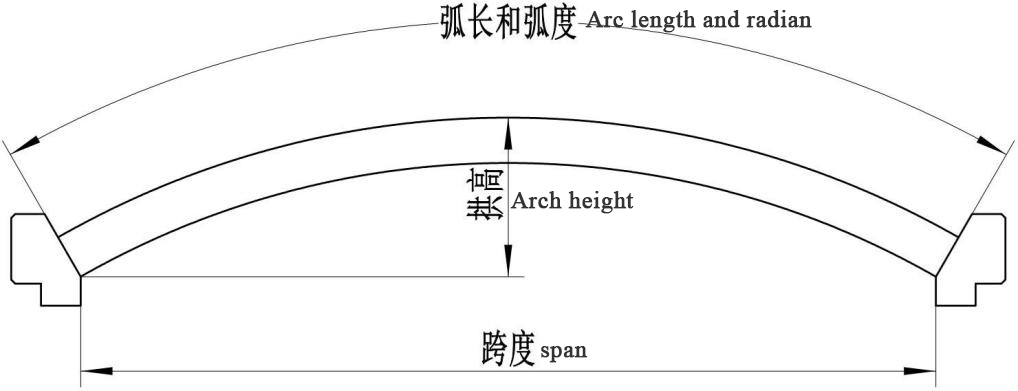
Typical structure of a fused cast crown.
First, to ensure consistency (Arc, Arch Height, Span) between each ring, refractory manufacturers must conduct pre-assembly in the factory. During pre-assembly, issues are identified and corrected. After meeting design requirements, alignment marks are sprayed on the bricks, and crown assembly data is recorded.
Pre-assembly is critical and is typically performed by experienced workers using specialized tools to avoid brick damage.
Pre-assembly is completed on an assembly platform equipped with clamping devices, supports, and crown templates.
Crown templates are essential tools for both pre-assembly and on-site construction. The same templates are used for both to ensure consistency. Common templates include steel, wooden, or earthen types (the latter is rare and not discussed here).
All templates must ensure reliability and stability.
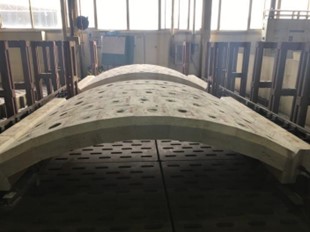
Pre-assembly of the crown by refractory manufacturers (steel template technique).
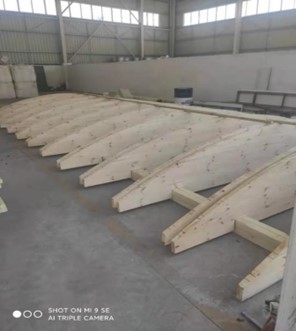
Wooden templates for crown assembly.
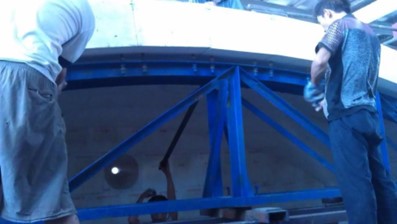
Construction of a fused cast crown using steel templates.
During construction, workers must follow pre-assembly data provided by the manufacturer. The first step is ensuring the template is level and plumb. When installing the final lock brick of each ring, consistent gaps and uniform "drop height" must be maintained to ensure consistent crown rise. (Drop height size: refers to the drop height of the arch height of the arch after the arch frame is removed during the construction of the arch)
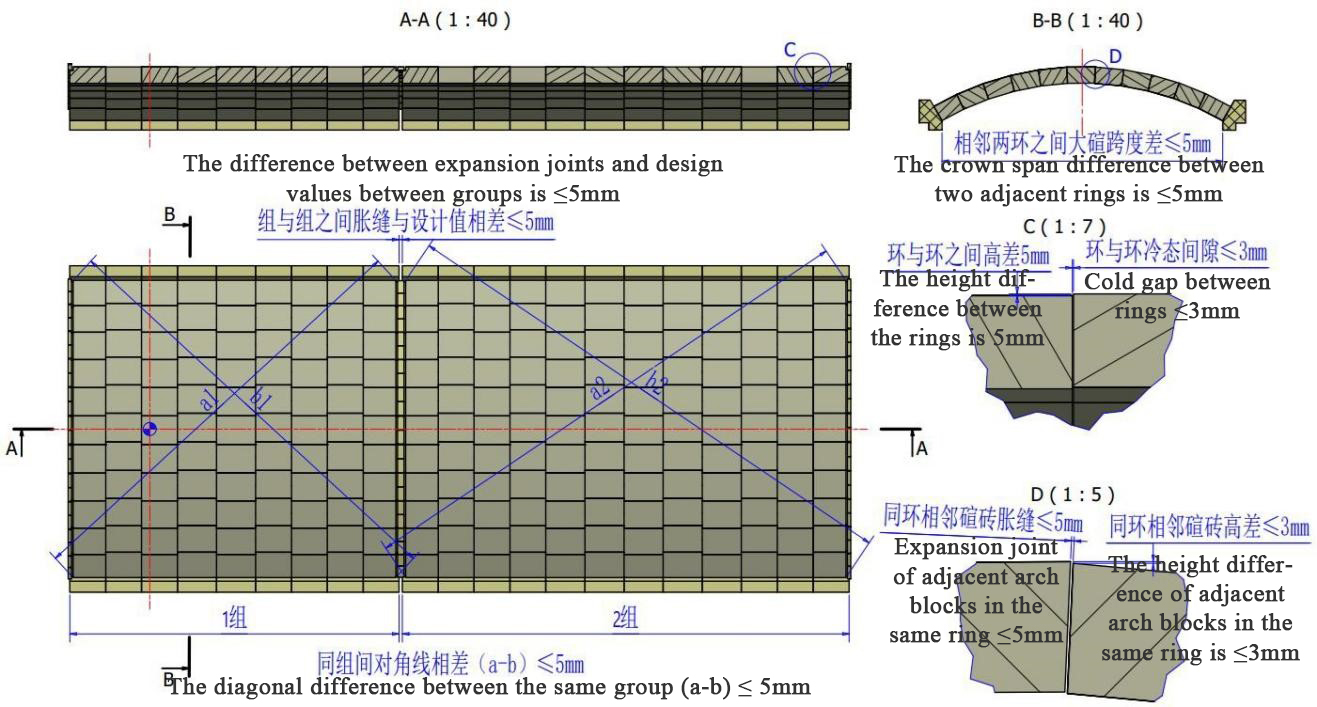
Key dimensional requirements for crown construction.
4. Heating-Up of Oxy-Fuel Glass furnaces
4.1 Characteristics of Heating-Up
Most oxy-fuel glass furnaces use hot-air heating-up. Some small glass furnaces may directly use oxy-fuel burners, but this is uncommon.
Hot-air heating-up, also called rapid heating-up, employs dedicated heaters to blow excess preheated air into the glass furnace. This technology emerged in the U.S. in the 1960s and was introduced to China in the mid-to-late 1980s, quickly gaining widespread adoption.
Compared to traditional methods, hot-air heating-up offers:
a) Uniform temperature distribution and even expansion;
b) Faster heating, saving time and fuel;
c) Precise temperature control (±2.5°C);
d) Reusable heating equipment;
e) Stable transition to main burners;
f) Positive-pressure heating, avoiding cold air-induced block cracking;
g) Enhanced glass furnace safety;
h) Easier automation.
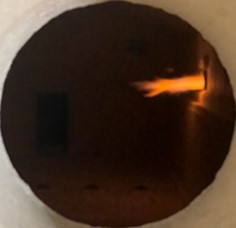
Hot air Furnace flame
4.2 Equipment for Hot-Air Heating-Up
a) Multiple heaters (quantity depends on glass furnace size/structure) with blowers;
b) Control cabinet (records temperatures, glass furnace pressure, adjusts blower frequency);
c) Burner pre-gun assembly (regulator valve, ball valve, needle valve for adjustment, check valve, flow meter);
d) Thermocouples and wiring;
e) Portable pressure gauge;
f) Handheld infrared thermometers (high/low temperature);
g) Mercury thermometers.
4.3 Tools for Heating-Up
a) Adjusting screws and wrench for tie rods;
b) Lever bars;
c) Wooden mallets;
d) Lubricants;
e) Flashlights;
f) Markers;
g) Measuring scales;
h) Chains and wires;
i) High-temperature blankets;
j) Welding/cutting tools;
k) Hooks (long/short).
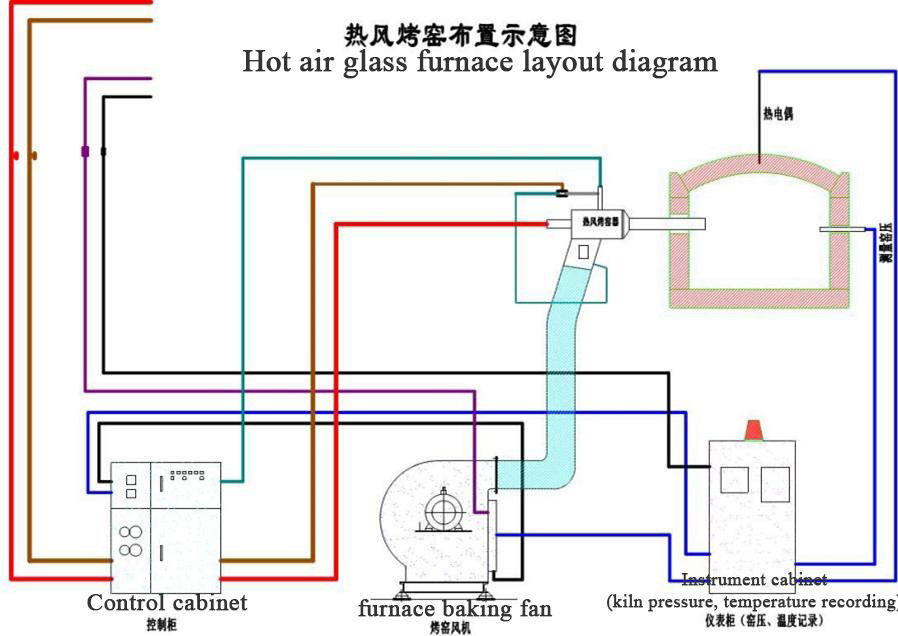
4.4 Adjustment of Steel Structures
Unlike traditional glass furnaces, adjustments focus on the crown‘s steel structure. Crown adjustments involve tie rod tensioning or screw adjustments, depending on glass furnace design and material choices.
The adjustment should be made according to the characteristics of different parts and different resistant materials combined with the heating curve. In principle, ensure diligent adjustment, less adjustment. Combined with the glass furnace worker‘s feeling of pulling strip and top wire tightening. Ensure that the tightness of the steel structure matches the expansion of the resistant material.
The adjustment of the steel structure of the crown should be combined with the arch height data and the degree of cracking in the upper part of the crown to ensure that the final crown bricks are upwardly open and the width of the openings is between 0-5mm. Please note that when the glass furnace heats up, the lower opening of the crown brick will cause the stress point of the crown to be concentrated in the upper part, which is very easy to cause the crown to collapse;
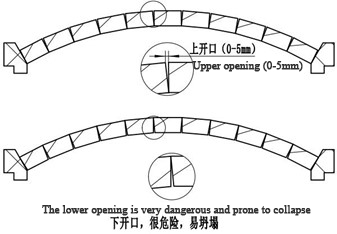
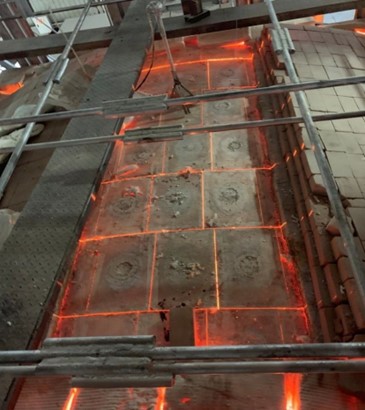
Top-opening in fused cast refractory crowns.
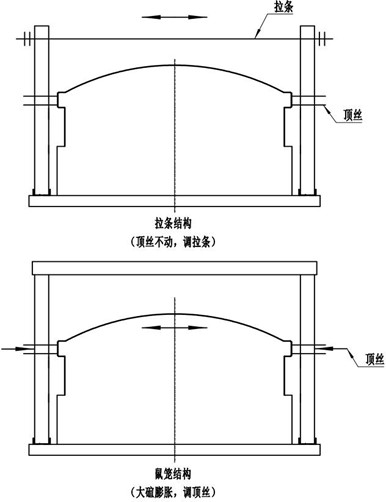
Two common steel support structures for crowns.
Crown adjustments are evaluated based on rise and top-opening data, with the final gap after heating-up serving as the benchmark.
4.5 Temperature Regime
According to the selection of refractory materials, a heating curve is formulated. Several nodes that need to be paid attention to include drainage stage, over-fire stage, refractory shrinkage and steel structure finalization stage.
a) 200℃ is the drainage stage, which mainly considers the removal of moisture inside the refractory material to avoid the block material from bursting when the temperature rises rapidly due to the accumulation of internal moisture. The drainage stage plans a 4–8-hour insulation time.
The sources of water inside the glass furnace are mainly from the following aspects:
- Cooling water during the processing of fused cast AZS blocks;
- Water in the mud during the glass furnace masonry;
- Water in the ramming material and castable material;
- Humid weather, moisture absorbed by the refractory material;
Different glass furnaces have different performances in the drainage stage due to different geographical locations, different masonry times, and different intervals between masonry completion and glass furnace baking. This requires close attention from on-site staff. There are even projects that have a large amount of drainage at more than 300 degrees. At this time, the glass furnace baking plan needs to be adjusted accordingly.
b) 1000℃ (±50℃) is the conventional over-fire stage (also called over-main fire). It is the process of switching the heating of the hot air glass furnace to the heating of the oxy-fuel burner, and generally 4 hours will be reserved. When switching, attention should be paid to the changes after the tail gas volume drops sharply. The operator should closely monitor the changes in the glass furnace pressure and adjust them in time. After switching to the main fire, due to the arrangement of the oxy-fuel combustion guns, in the case of multiple guns, the glass furnace temperature should be balanced as much as possible to avoid local temperature being too high or too low, which will affect the overall expansion of the glass furnace.
c) 1300-1350℃ is the stage of steel structure finalization and zirconium sealing material sintering (some molten casting materials have an obvious shrinkage stage during this period, and close attention must be paid when adjusting the steel structure). Generally, it is planned to keep warm for 8 hours. The steel structure is basically finalized after this, and no adjustment is made to the steel structure except for individual parts.
d) 1350-1600℃ is the feeding stage (determined by different products). There are manual pushing and blowing modes for feeding. When the liquid level rises to 300mm from the production level, the feeder can be switched to feed and consider changing from full broken glass to broken glass plus powder batching mode, so as to normalize production as soon as possible.
e) Before some glass furnaces are put into production, we will arrange a certain period of stuffing, usually about 8 hours. There are also some factories that directly discharge materials without going through the stuffing stage, which will not be repeated here.
4.6 About the heating rate
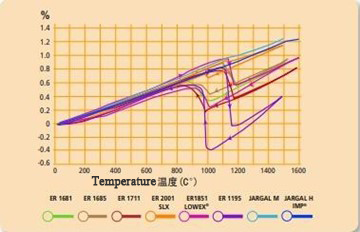
Expansion curves of commonly used casting materials (typical values)
The heating rate is formulated taking into account the expansion characteristics of the main materials. The above figure is the expansion curve of commonly used casting materials in oxyfuel furnaces. The temperature rise should be stable at key points, and sufficient time should be left for steel structure adjustment.
Due to different processes and materials, the expansion curves of some small refractory suppliers will deviate from the above figure. This needs to be considered when formulating the heating curve during the preparation stage of the glass furnace. When baking the glass furnace, the on-site engineers should adjust the glass furnace baking progress in time according to the specific situation. These experiences require long-term accumulation.
4.7 Countermeasures for abnormal situations
a) A project in 2011 due to incorrect thermocouple indexing connection. This causes a large deviation between the glass furnace display temperature and the actual temperature. The direct manifestation was that most of the pull rods were locked and could not be loosened, and the crown continued to rise. The measures taken at this time were to stop heating and heat preservation for 36 hours, strengthen the insulation of the exposed refractory materials, and continue heating after the temperature was consistent.
b) In 2021, a factory used fused cast AZS block materials produced by a small factory. Due to its poor quality, the crown was very different from the theoretical curve when it expanded. Finally, under the precise monitoring of the on-site engineer, the heating plan was adjusted many times, and the glass furnace baking target was basically achieved.
c) In a project in 2018, because the factory was located in the south and the glass furnace was baked directly after the glass furnace was built, the water discharge at the bottom of the glass furnace was large at more than 200 degrees. It was solved by extending the drainage time.
5. Thermal insulation of oxy-fuel glass furnaces
5.1 Thermal insulation characteristics of oxy-fuel glass furnaces
a) Treatment of expansion joints
The treatment of sintering materials and insulation materials of oxy-fuel glass furnaces is basically the same as that of traditional glass furnaces. Here, it mainly refers to the treatment of expansion joints of molten casting materials.
Different design units should fully consider the expansion characteristics of materials when designing the structure of molten casting materials, and reserve appropriate margins during design. If the margin is too large, it is not easy to swell in the later treatment, which is difficult to handle. The glass furnace is prone to fire at this point due to long-term high glass furnace pressure; if the reserved expansion amount is too small, it is easy to swell in the glass furnace, and it may arch in severe cases, making later heat treatment more difficult.
As a construction unit, in order to handle the expansion joints well, special attention should be paid to the selection of materials, construction sequence, and treatment nodes.
b) Thermal insulation coatings
As the last barrier of glass furnace insulation, the application of thermal insulation coatings plays a very important role. Proper use of thermal insulation coatings has a very obvious effect on the energy saving of glass furnaces.
Due to excessive competition, the quality and price of thermal insulation coatings on the market are uneven.
The thermal insulation coating should be applied after the glass furnace is charged. At this time, the steel structure of the glass furnace has been finalized and will not change significantly. The thermal insulation coating will be relatively stable after application and can achieve the expected purpose.
Construction focus:
- In addition to covering a large area, covering the side stubble is equally important;
- During facade construction, it should be applied multiple times.
- The construction thickness depends on the design requirements and the quality of the thermal insulation coating. Generally, it is 30-150mm.
5.2 Later operation and maintenance
Since the water vapor concentration in the exhaust gas of the oxyfuel glass furnace is much higher than that of the traditional air-assisted glass furnace, the viscosity of the glass surface will be relatively smaller. In addition, in order to increase the melting rate, the local temperature is relatively high. In the later operation and maintenance of the glass furnace, special attention should be paid to the glass squeezing phenomenon in the block joints of the sidewall. If the problem is found, it should be solved as soon as possible to avoid long-term delay.
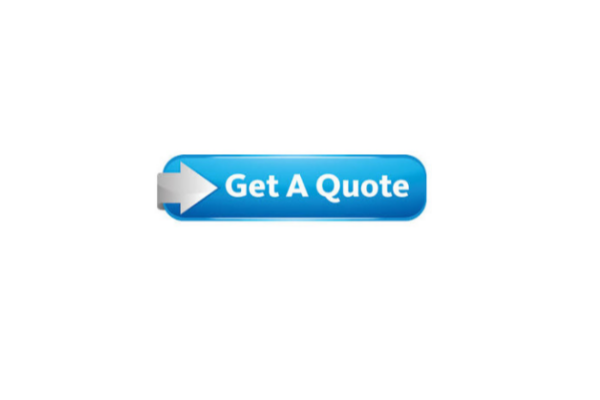
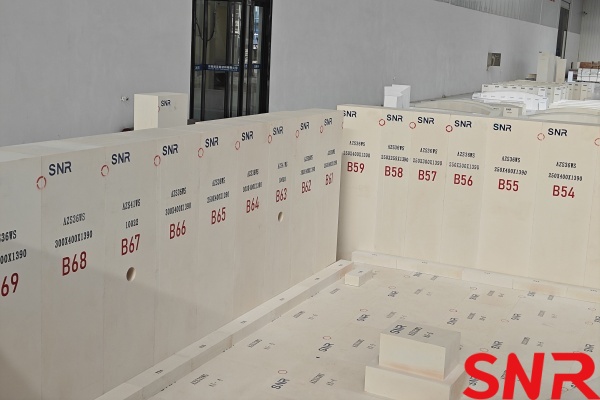
6. Outlook
For oxyfuel glass furnaces, since the flame space is mostly dry-laid with fused cast AZS refractory materials. Therefore, it puts forward higher requirements on the treatment of expansion joints and the adjustment of steel structures during glass furnace baking. Although the temperature inside the glass furnace will be relatively balanced when the hot air glass furnace uses a large air volume to assist combustion. However, with the continuous development of special glass furnaces, it puts forward higher requirements on glass furnace masonry and glass furnace baking technology.
6.1 Progress in glass furnace baking technology
►Arrange more glass furnace heaters;
According to the structure of the glass furnace, in order to obtain a more balanced temperature, more glass furnace heaters are usually installed in more parts of the glass furnace, and the glass furnace heaters are adjusted individually based on the information of the temperature measurement points in order to obtain more uniform temperature rise data.
►Automatic control system;
The new glass furnace system uses more detection points (including more dense thermocouples, glass furnace pressure, and optical pyrometers) to provide a more accurate basis.
The automatic control system will automatically adjust the fuel consumption and fan air volume of the glass furnace heaters at different locations based on the data collected by the system from various parts of the glass furnace. When the target temperature exceeds the set temperature rise plan, the system will issue an alarm to notify the on-site personnel to intervene manually.
6.2 Application of new technologies
►Application of electrode coating
The original molybdenum electrode usually starts to push the electrode into place after the glass liquid level reaches the predetermined position. However, as plate electrodes and mushroom head electrodes, they must be pre-installed inside the glass furnace or the material channel. The previous practice was to cover them with glass fiber cloth and water glass, but this has certain risks. There are also projects that fill the glass furnace with broken glass before baking the glass furnace. The advantage of this is that it can perfectly protect the electrode from oxidation. The disadvantage is that the glass furnace baking time is extremely long and the cost cannot be effectively controlled.
When high-temperature coating technology comes, these problems are solved. At present, many domestic companies have mastered the high-temperature coating technology of electrodes, which provides more options for the development of special glass furnaces.
►Application of internal coating of refractory materials
The internal coating technology of glass furnaces has been developed in recent years. It mainly uses nanomolecular materials to spray the inside of the glass furnace
(mainly the refractory material in the glass furnace flame space). It can increase the heat reflection ability, increase the surface density of refractory materials, reduce the erosion rate, and extend the life of the glass furnace.
Currently known spray materials include silicon, corundum, zirconium corundum, and aluminum silicon for actual combat use. For more details, please consult a professional team.
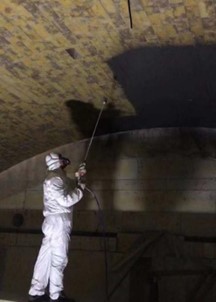
Spraying construction of crown
History is developing and technology is improving. As more and more people of insight invest in the field of oxyfuel combustion technology, oxyfuel combustion glass furnaces will surely develop rapidly in the glass industry, and will also give rise to more advanced technologies and equipment applications. Lower energy consumption, lower emissions, better product quality, better economic benefits, longer glass furnace life, and more reasonable construction and operating costs are our constant goals.
Henan SNR Refractory Co., Ltd. is dedicated to the manufacturing research and development of fused cast AZS refractory materials for the glass industry. Meanwhile, SNR can provide total solutions and services for glass furnace design, glass furnace construction, renovation, and upgrading. Please contact me if you have any requirements.
CONTACT: zoe@snrefractory.com
WEBSITE: www.snr-azs.com